Inventory Control
Productivity Enhancement | November 25, 2020
Managing inventory is very important aspect of the business and it cannot be ignored. Final product, raw materials used in production and semi-finished goods in warehouse can be categorised as inventory.
Maintenance, repairing and operating (MRO) supplies are also classified as inventory and it is most relevant for manufacturing industries. MRO supplies play a vital role in the day-to-day functioning of an organisation.
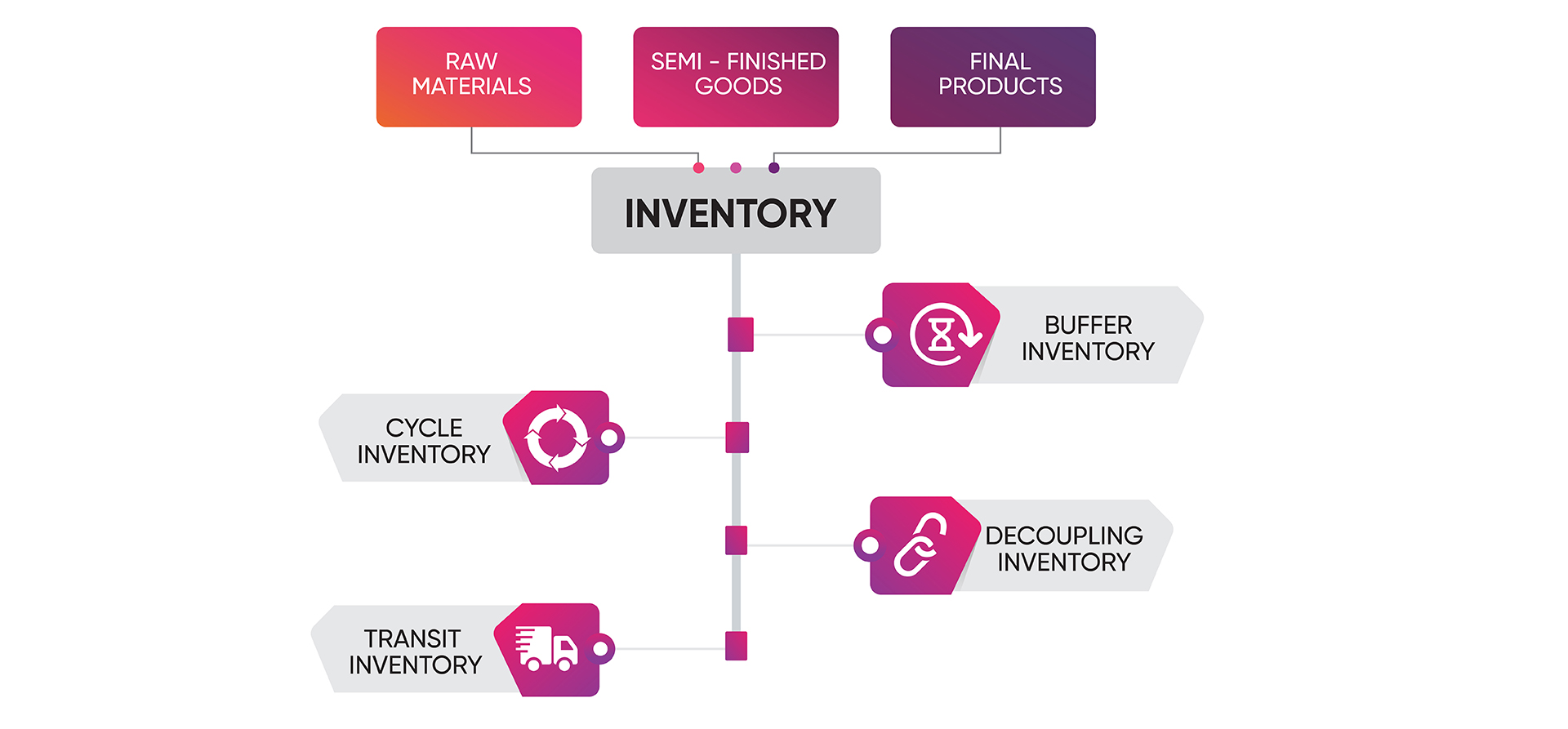
Inventory – Types
Uncertainty in certain factors can be managed by maintaining the buffer inventory, also called as the safety stock. Those items categorised as buffer inventory is stored in warehouse or factory, to bear the brunt of unexpected situations. Any untoward situation like delay in transport, rise in demand or labour issues can be managed if sufficient buffer inventory is maintained.
Cycle inventory, decoupling inventory and transit inventory are the other types of inventory.
While cycle inventory refers to stocking of items that are continuously used in production, decoupling inventory means having stock of unfinished products at each stage of the production cycle so that the plant continues to produce output even if one part of the plant stops functioning. Items that are being moved from one place to another is called transit inventory.
Original equipment manufacturers know every part of the equipment that they have manufactured and so it is best to rely on them for your spare parts inventory management.
OEMs have through years of experience gained knowledge about the types of replacement or consumable parts that are frequently needed and in what quantities.
Propel Industries helps the customers to create a customised inventory plan so that parts that are needed are readily available, the downtime is reduced and productivity is enhanced.
First in, first out
First in, first out inventory management system involves selling older products first so that any financial loss can be prevented in case the products become obsolete. It is a general belief that businesses using FIFO are more profitable when compared to other methods.
Closing remarks
- It is important to stock up minimum inventory for every single machine that you possess. This will increase the availability of machine. Parts can be replaced faster if minimum stock is available, in-house. Housekeeping and accessibility are other two important aspects that must be kept in mind.
- This reduces the shipment time of consumables and wear parts.
- The time taken for maintenance will also be reduced.