In-depth – Track Mounted Screen 1861 (4Deck)
Inside-Out | December 8, 2021
The Track Mounted Screen from Propel Industries has the best of both technology and engineering expertise. The high-engineered huck bolt fastening system has been proved to be a safe and reliable method.
Track mounted Screen TMS 1861 is made up of following parts –
- Screen
- Chassis
- Main Conveyor
- Side Conveyors
- Oversize Conveyor
- Mid Oversize Conveyor
- Tail Conveyor
- Motorised pulley
- Engine package
- Diesel tank
- Hydraulic control unit
- Hydraulic power pack
- Crawler
- Radio remote control
- Change over switch panel
- Electrical control panel (IP55)
- Engine controller (DSE4520 series)
Let us now understand the key aspects of each component.
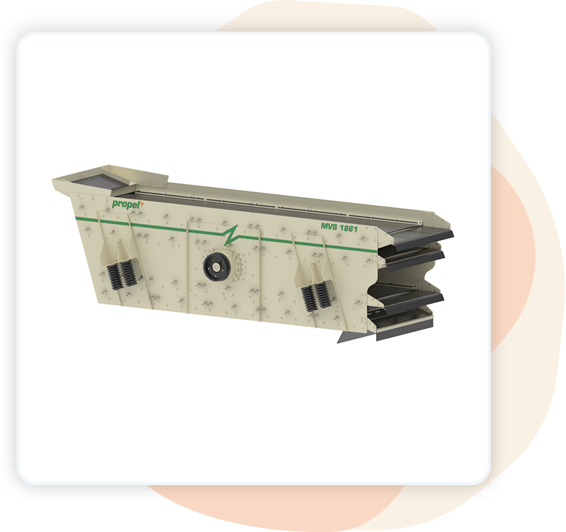
Screen
Propel Vibrating Screen 1861 is a 5 product mobile screen with effective screening area of 9.5 m2 in each deck. Circular motion screen handles maximum feed size upto 150 mm and handles material capacity upto 600 TPH in feed.
Chassis
Heavy duty I-section welded construction provides maximum strength & accessibility and the design includes spacious walkway, ladder, guard rail & hand rail which increases easy accessibility ensuring safety (EHS).
Mobile machinery is provided with light mast for better visibility to access the control station.
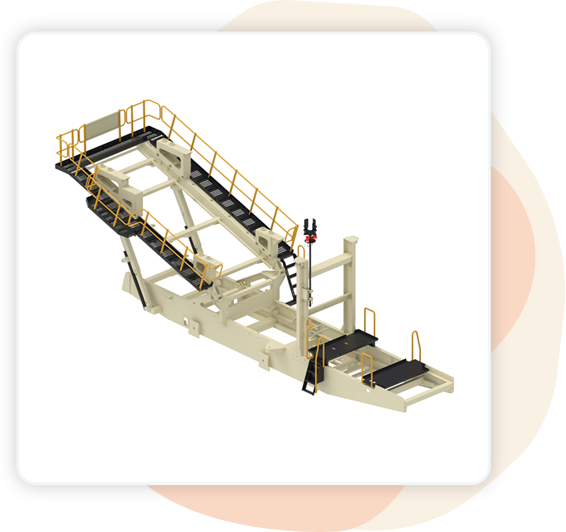
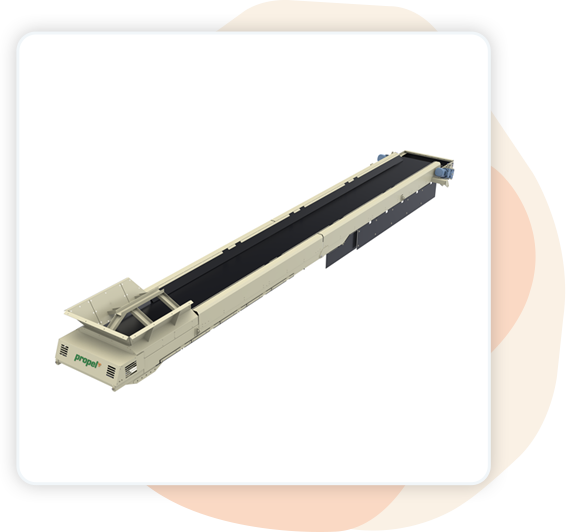
Main Conveyor
The main conveyor is responsible for conveying materials from feed conveyor to screen.
Side conveyors
Materials from the third and fourth deck screen are moved out as end product by the side conveyors.
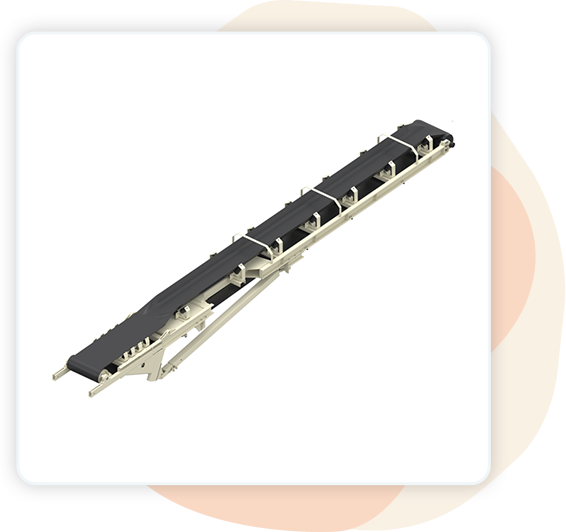

Oversize conveyor
The oversize conveyor conveys the materials from first deck screen to cone crusher/ VSI equipment for recycling.
Mid oversize Conveyor
Materials from the second deck screen are moved out as end product by the mid oversize conveyor.
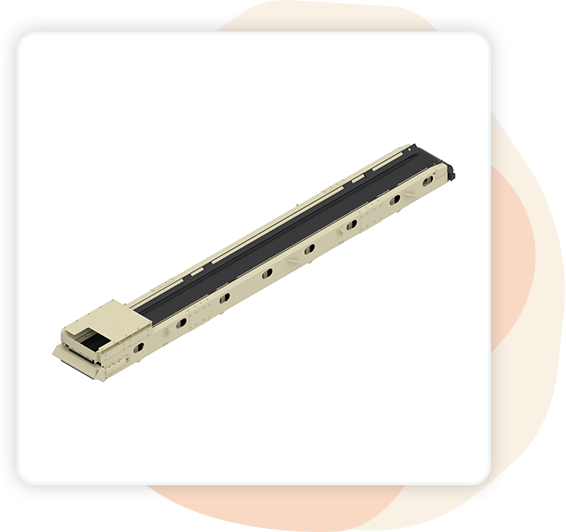
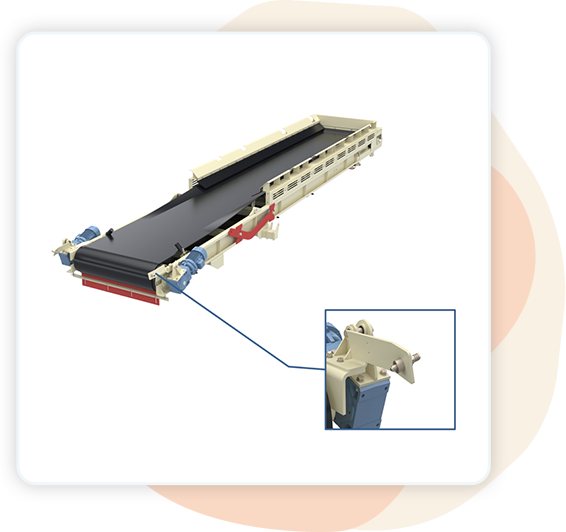
Tail conveyor
The tail conveyor conveys fine materials as an end product. Dust suppression with atomiser nozzles mounted on the conveyor discharge points help in minimising air pollution (EHS). It is attached to an outlet manifold of water pump for pressured water supply.
Motorized Pulley
All conveyors are attached with motorized pulley. Up to 95% of the output power produced by the motor is typically transmitted to the drum shell and it consumes less space and is completely free from water, dust, chemicals, grease, oil, etc.
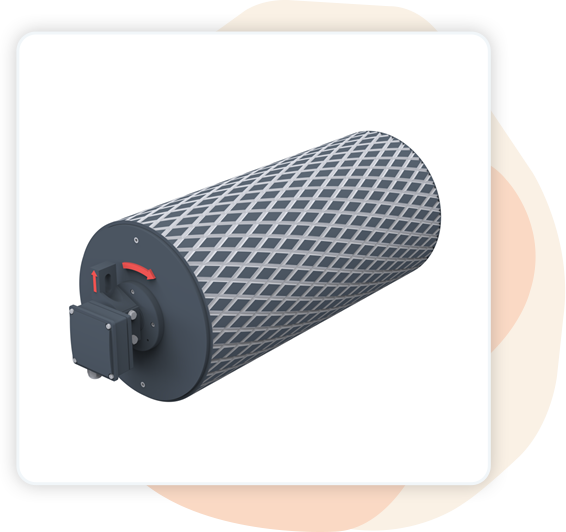
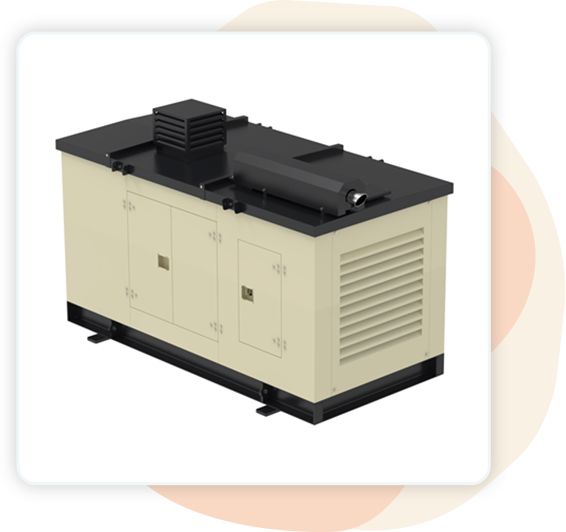
Engine Package
The engine package consists of the engine and the alternator. This powers the entire equipment and safeguards it from dust, noise and rain.
Diesel Tank
The diesel tank is used to store fuel for engine consumption. It is equipped with a level sensing, with suitable filler and a breather.
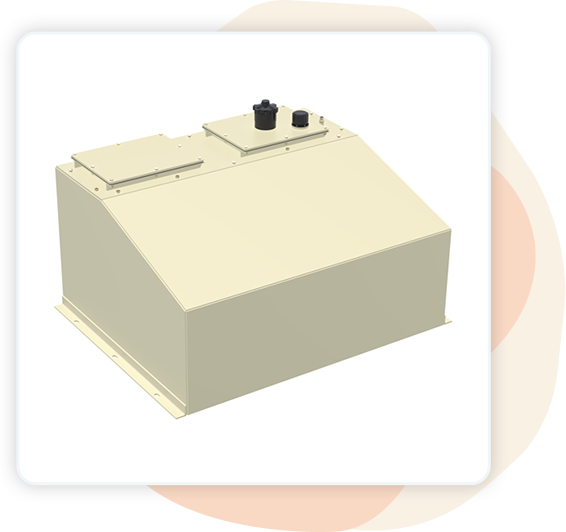
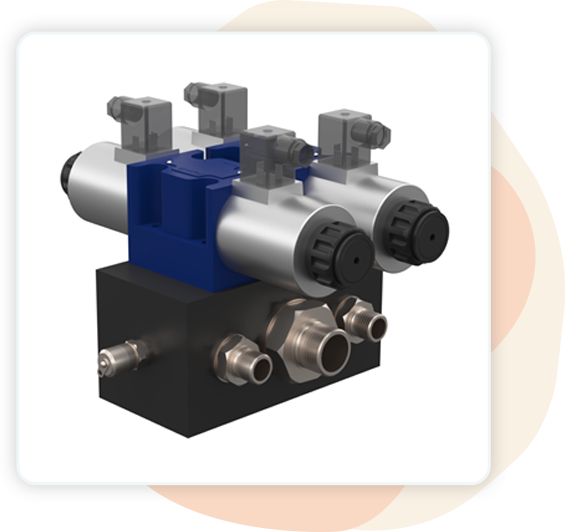
Hydraulic Control Unit
The Hydraulic control unit generates and adjusts hydraulic pressure and switches its passage. The control unit provides several pressure levels. The line pressure control valve is governed by a solenoid and controls line pressure.
Hydraulic Power pack
The purpose of the hydraulic reservoir is to hold a volume of fluid, transfer heat from the system, allow solid contaminants to settle down and also facilitate the release of air and moisture from the fluid. The capacity of the hydraulic tank is 400 litres.
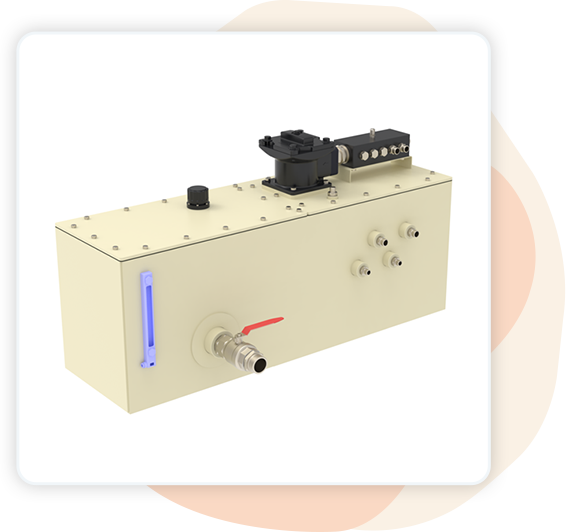
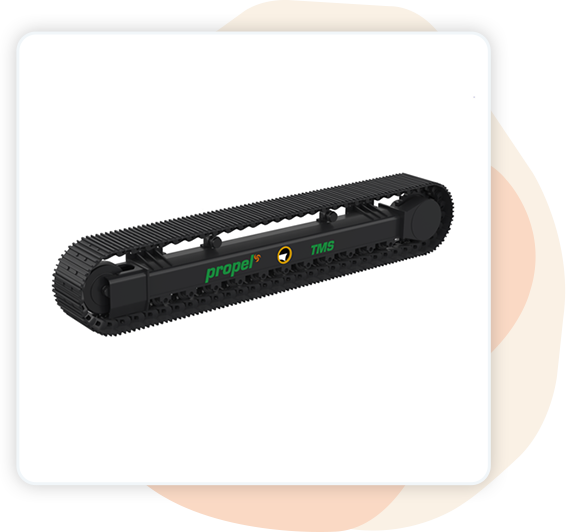
Crawler
The undercarriage is the part of a moving vehicle that is underneath the main body of the vehicle. Crawlers are heavy-duty machines specifically developed for the transport and relocation of heavy mining equipment or processing plant equipment.
Radio Remote Controller
The Radio remote Controller is used as application for track crawler movement. In a radio control system, when a command is transmitted from the operator to the receiver (located in the control panel), the radio signal is transmitted to a distance of 50m around the machine.
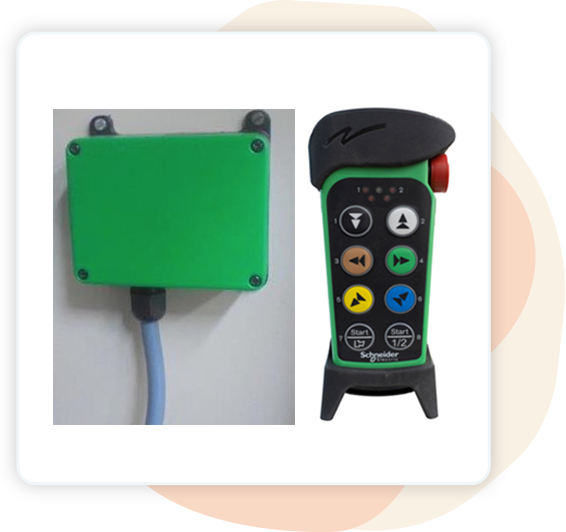
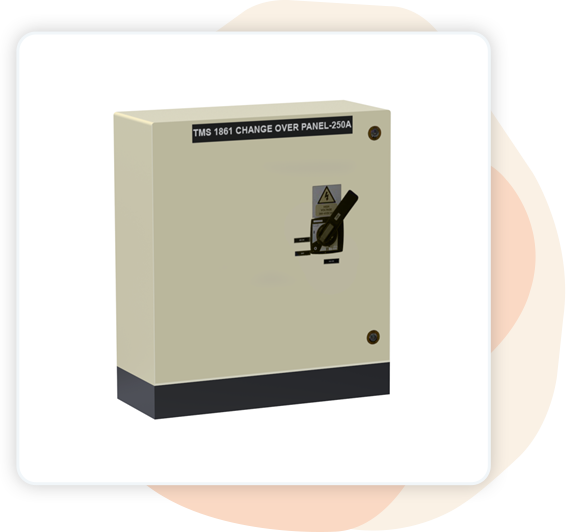
Change Over Switch Panel
There is an option for dual power mode. This gives flexibility to power the plant either by external electric connection or by on-board diesel generator power pack unit.
Electrical Control Panel
The electrical control panel has been designed with a double door to make it dust proof and water proof. It comes with IP55 certification and it is mounted onto the machine. The machine is controlled by electrical operation through the operating panel. The operation is manual, though auto mode functions have also been implemented in the panel. While manual operation happens through illuminated push buttons, auto mode operation is controlled by the HMI display.
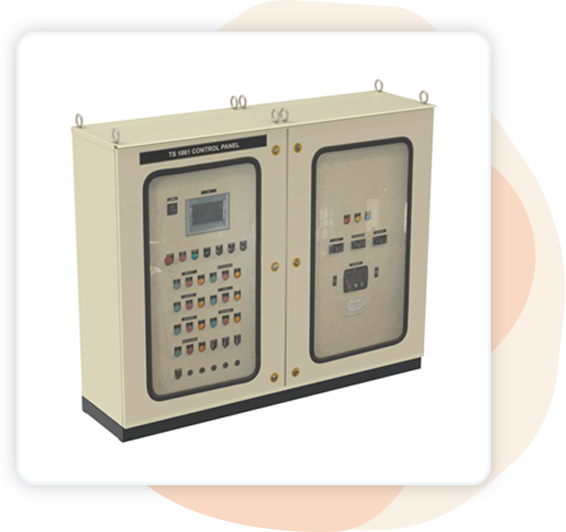
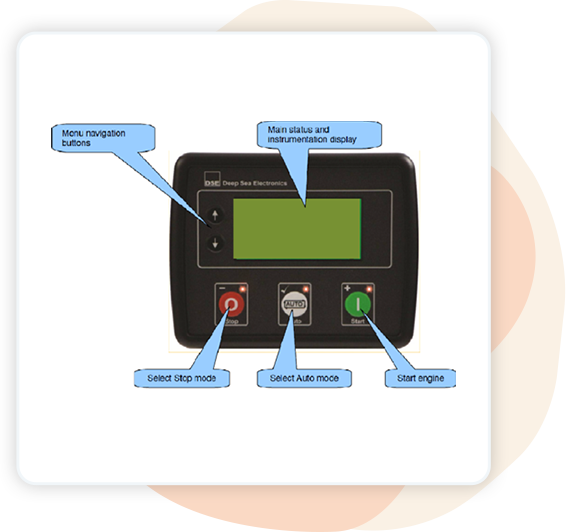
Engine Controller (DSE4520 SERIES)
The engine controller device controls the engine start/stop. Electrical parameters which have been set as per our applications, is shown in the display.