In-depth – Track Mounted Jaw Crusher 811(S)
Inside-Out | July 27, 2021
The TMJ series single toggle Jaw crushers from Propel has been widely accepted and appreciated by the customers. Here are the reasons
- The elevated mouth opening ensures significant production by eliminating frequent bridging of stone in feed opening.
- The optimum jaw nip angle reduces the laminar product shape ensuring even manganese wear-off with increasing production.
The TMJ series single toggle Jaw crusher is made up of the following parts
- Jaw crusher
- Hopper
- Grizzly feeder
- Chassis
- Main conveyor
- Scalp Chute
- Scalp Conveyor
- Motorised pulley
- Engine package
- Diesel Tank
- Hydraulic control unit
- Hydraulic powerpack
- Crawler
- Radio remote control
- Change over switch
- Electrical control panel
- Engine controller
Let us now understand the key aspects of each component.
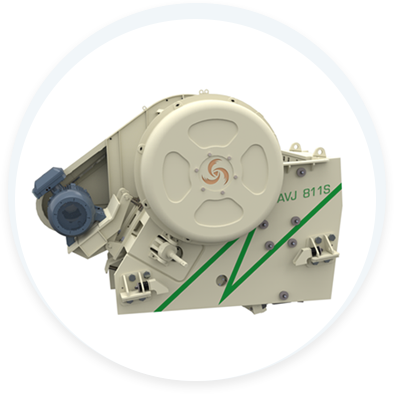
Jaw Crusher
Features of Propel AVJ series single toggle Jaw Crusher
- It offers maximum possible fatigue strength and best reliability as it comes with various mounting possibilities.
- The fully-welded sturdy construction results in lowering the production cost per ton.
Hopper
The primary hopper is
- Used to store materials that are fed by dump hoppers of back loaders or excavators.
- It is hydraulically foldable with a capacity of 8 m3.
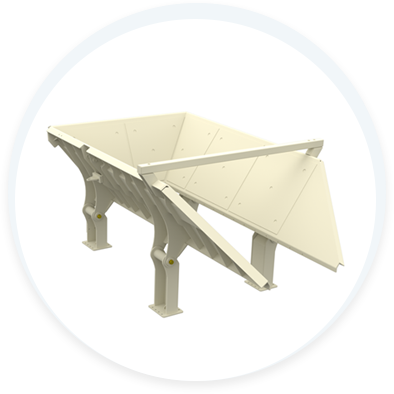
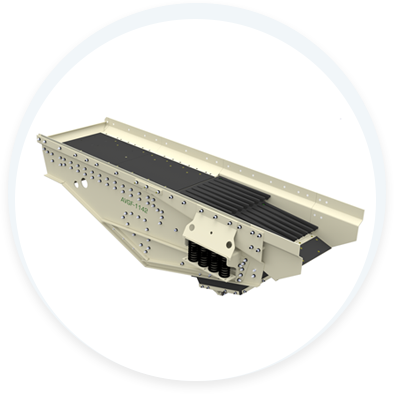
Grizzly Feeder
The Grizzly feeder from Propel can
- Handle large feed rate with coarse blasted rock, apart from the material impact from dump trucks or wheel loaders
- Its step height and tapered grizzly bars eliminate pegging and thus enhances the efficiency of separation.
Chassis
The heavy duty I-section welded construction provides maximum strength and is also great for accessibility.
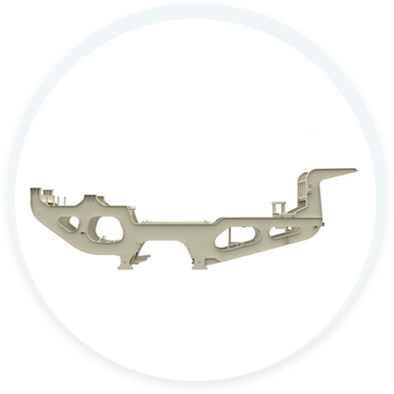
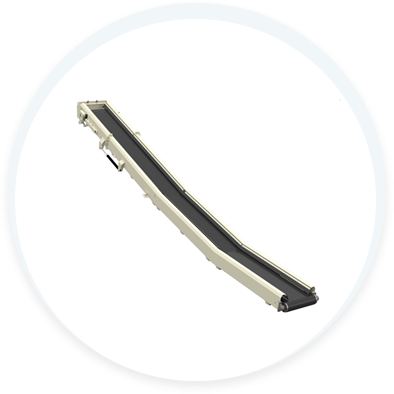
Main Conveyor
The Grizzly feeder from Propel can
- The main conveyor does a great job of conveying materials from jaw crusher and first deck materials of grizzly feeder to the secondary stage.
- The cone crusher feed conveyor and vibrating grid of track screen can be classic examples of main conveyor.
Scalp Chute
The work of a scalp chute is to transfer fine materials screened by grizzly feeder into a scalp conveyor.
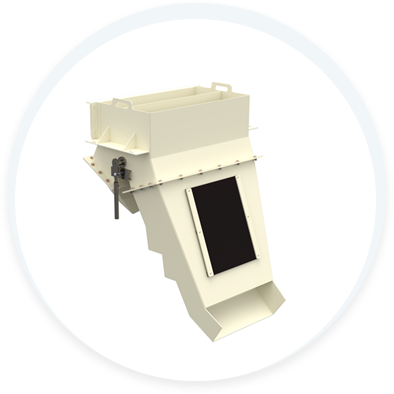
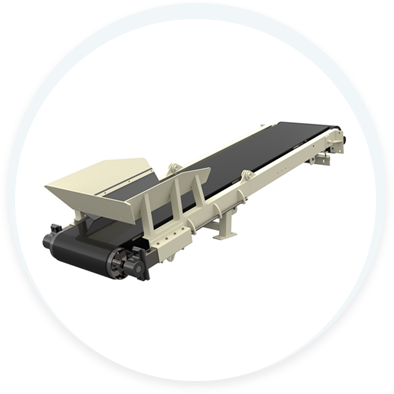
Scalp Conveyor
The scalp conveyor’s job is to convey the fine materials.
Motorized Pulley
The main conveyor and the scalp conveyor are attached to the motorised pulley. It is interesting to note that upto 95% of the output power produced by the motor is typically transmitted to the drum shell. The motorised pulley occupies lesser space and is protected from water, dust, chemicals, grease and oil.
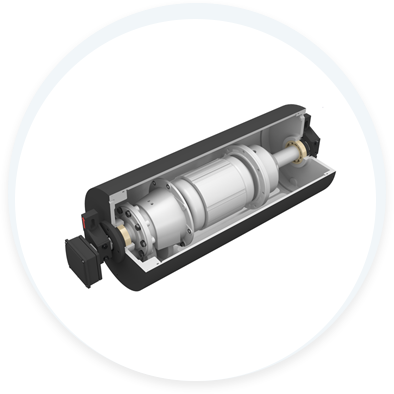
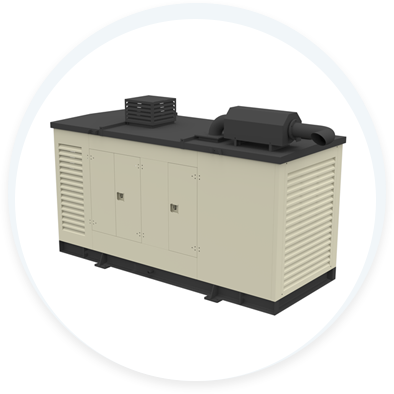
Engine Package
- The engine package consists of the engine and the alternator, which together powers the entire equipment.
- Its design protects the engine package from dust, noise and rain.
Diesel Tank
- The diesel tank is used to store diesel for engine consumption. It is equipped with a level sensing and a filler breather.
- The capacity of the diesel tank is 500 litres.
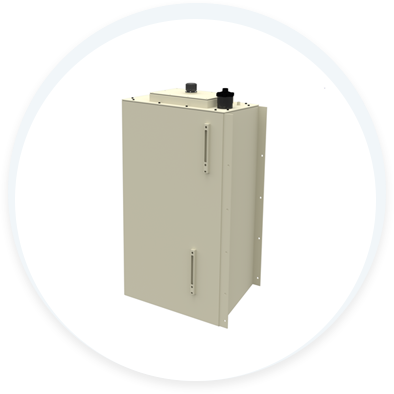
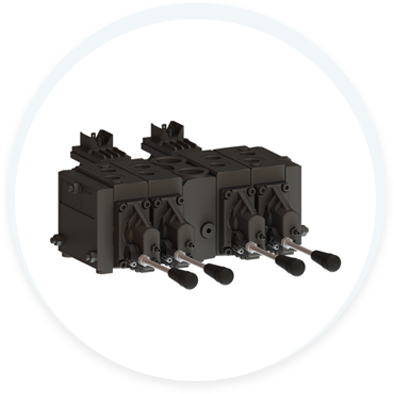
Hydraulic Control Unit
The hydraulic control unit generates and adjusts the hydraulic pressure and chooses its passage. The unit provides several pressure levels with varying options. The solenoid in the line pressure control valve controls the line pressure.
Hydraulic Powerpack
The hydraulic reservoir performs the following functions
- It hold a volume of fluid
- Transfers heat from the system
- Allows solid contaminants to settle
- Facilitates the release of air and moisture from the fluid
The capacity of the hydraulic tank is 400 litres.
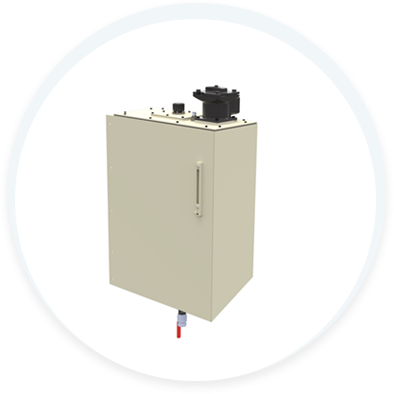
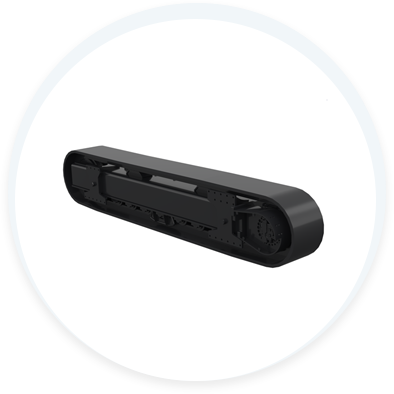
Crawler
As the name reveals, the undercarriage (or the crawler) which is part of a moving vehicle, is underneath the main body of the vehicle. Crawlers are heavy duty machines which are specifically developed for the transportation and relocation of heavy mining equipment or processing plant equipment.
Radio Remote control
The radio remote control is used for moving the track crawler and for start/stop operation of the grizzly feeder. When a command is transmitted from the operator to the receiver (located in the control panel), the radio signal is then transmitted to a distance of approximately 50m from the machine.
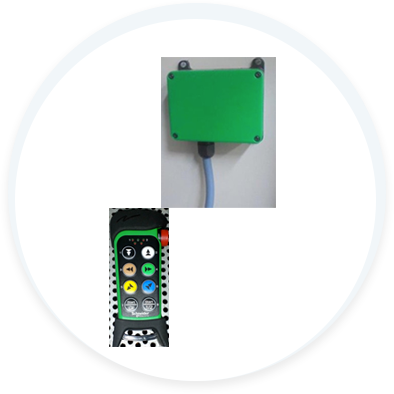
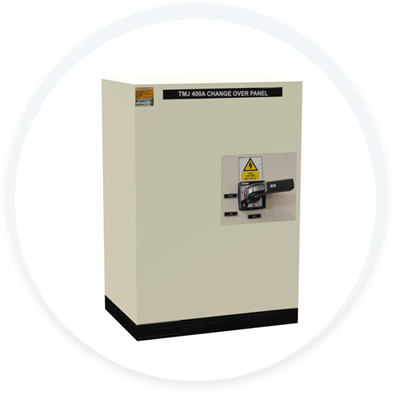
Change Over Switch
The change over switch is designed to transfer electricity from the commercial power grid to a local generator when outage occurs. This is also known as transfer switches. They connect directly to the generator, commercial power supply or the line.
Electrical Control Panel
The electrical control panel is designed with a double door which gives it the dustproof and water proof features. It is IP55 certified and is mounted on the machine. The machine is controlled by electrical operation through the operating panel.
It can be operated through manual mode. The auto mode helps the panel function. Illuminated push buttons make the operator follow the manual operation easily. The functioning of the auto mode operations can be seen by HMI display.
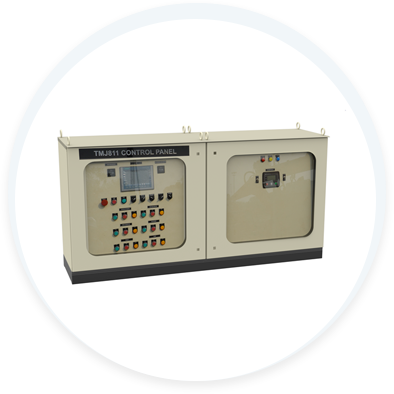
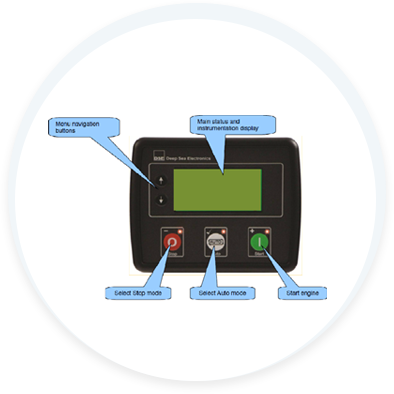
Engine Controller (DSE4520 SERIES)
The engine controller controls the start/stop of the engine. The electrical parameters that are shown in the display can be set as per the requirements.
~ S. Prashanth, G. Prabhakaran and B.Govindaraj