In- depth – Components of a Jaw Crusher
Inside-Out | June 14, 2021
The jaw crusher is one of the most admired and most sought after equipment from the house of Propel Industries. For the benefit of newcomers in the industry, here is an explainer of the various components of the Jaw crusher.
A jaw crusher consists of
- Crusher Body
- Pitman
- Jaw plate
- Rear end frame
- Eccentric shaft
- Flywheel
- Jaw crusher bearings
- Toggle plant
- Retraction spring and screw rod
- Check plate
- Setting adjustment
1. Crusher Body
The design of the crushing body ensures that it is capable of exhibiting resistant to bending stress even when the crushing hard materials.
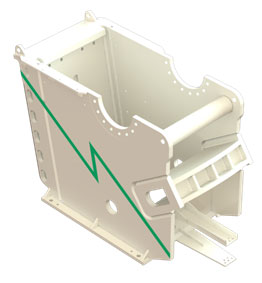
2. Pitman
The pitman usually denotes a connecting rod, but in a jaw crusher it does not connect two things. Here, it refers to the moving jaw in a jaw crusher. It achieves the reciprocating movement through the eccentric motion of the flywheel shaft. This creates enormous force in each stroke. The pitman is fitted with two replaceable high strength steel alloy toggle plate.
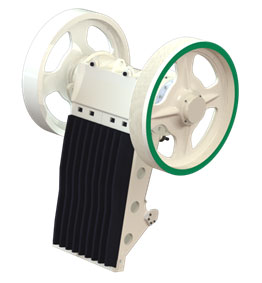
3. Jaw Plate
The inward facing side of the jaw crusher pitman is covered with a jaw plate made of manganese which is an extremely hard metal. The jaw plates are usually symmetrical from top to bottom and can be used on either side. This comes handy as the wear occurs at the bottom (closed side) of the jaw and flipping them over provides another equal period of use before they can be replaced.
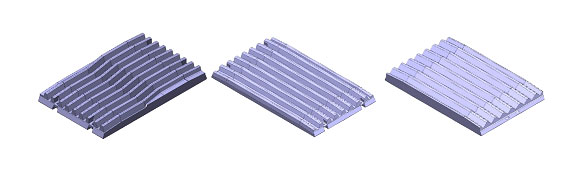
4. Rear end frame
The fixed jaw face is opposite to the pitman face and is statically mounted. It is also covered with a manganese jaw plate. Manganese liners (Jaw plate) protects the frame from wear. These include the main jaw plates covering the frame opposite the moving jaw and the cheek plates which line the sides of the crusher body within the crushing chamber.
5. Eccentric Shaft
The pitman is put in motion by the oscillation of an eccentricity on a shaft that goes through the pitman's entire length. This force is also put on the shaft itself so they are constructed with large dimensions and with hardened steel. The main shaft that rotates has a large flywheel mounted on each end. Its eccentric shape initiates the movement of the moving jaw in and out. The eccentric shaft is made of Alloy Steel Fitted with anti-friction bearings and is in the pitman and dust proof housing.
6. Flywheel
The rotational energy is fed into the eccentric shaft of the jaw crusher by means of a sheave pulley which usually has multiple V-belt grooves. In addition to turning the pitman, eccentric shaft usually has substantial mass to help maintain rotational inertia as the jaw crushes the material.
7. Jaw Crusher Bearings
There are typically four bearings on the eccentric shaft: two on each side of the jaw frame supporting the shaft and two at each end of the pitman. These bearings are typically roller in style and usually have labyrinth seals and some are lubricated with an oil bath system.
The bearings that support the main shaft normally are spherical tapered roller bearings on an overhead eccentric jaw crusher.8. Toggle Plate
The bottom of the pitman is supported by a curved piece of metal called the toggle plate. It allows the bottom of the pitman to move up and down with the motion of the eccentric shaft, apart from serving as a safety mechanism for the entire jaw. The piece of non-crushable material such as a steel loader tooth (sometimes called "tramp iron") enters the jaw crushing chamber and being larger than the closed side setting it can't be crushed nor can it pass through the jaw. In this case, the toggle plate will bend or break thus preventing further damage.
9. Retraction spring & Screw rod
Without the spring & retraction screw rod, the bottom of the pitman would just flop around as it isn't connected to the toggle plate and is just resting against it in the toggle seat. The retraction screw rod system ensures the pitman is firmly fixed to the toggle plate. It is designed to fail before any damage occurs to the crusher body, pitman or shaft. The toggle seats are fixed points where the toggle plate contacts the pitman and the toggle beam.
10. Cheek Plates
The sides of the crusher body are covered with cheek plates. It is made of high-strength manganese steel plates and are wear resistant.
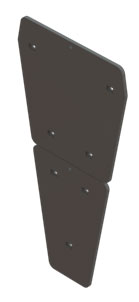
11. Setting adjustment
Varying material output size (discharge) is achieved by adjusting the opening at the bottom of the jaw, commonly referred to as the "closed side setting". This can be done by inserting shim plates, wedge movement and hydraulic system.
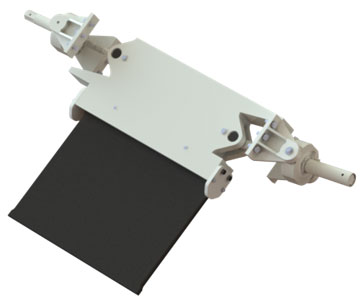
~ L Ravi Siddharth