In depth – Avc Cone Crusher
Inside-Out | April 29, 2022
In the last issue, the In-Depth column focused on Jaw Crusher. This time, the spotlight turns on to our Cone Crusher. Some of the factors that R&D department considered before getting to make the Cone Crusher
- The product must meet the customer’s unique requirement.
- Cutting – edge technology must be put to work.
- The product must cater to the 100 TPH to 350 TPH segment and serve the crushing industry.
- The product must be in a position to evolve.
CONE CRUSHER MODEL
- AVC 125 / AVC 160 / AVC 220 / AVC 250 / AVC 350
- SM 100 / SM 150 / SM 200 / SM 250
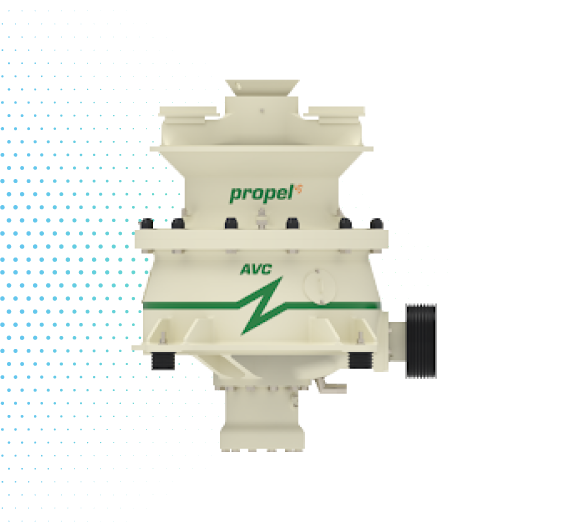
Cone crushers are used in the mineral, mining, and aggregate industry for fragmentation and production of rock materials. Cone crushers are the most commonly used crusher type for the secondary and tertiary crushing stages. AVC Cone Crushers can be easily adjusted to different types of production requirements with change of chambers, eccentric strokes, and counter shaft speeds.
CONE CRUSHER WORKING PRINCIPLE
- Both cone and gyratory crushers have an oscillating shaft.
- The material is crushed in a crushing cavity, between an external static element (Concave) and an inner moving element (Mantle) mounted on the oscillating shaft assembly.
- An eccentric shaft rotated by a gear and pinion produces the oscillating movement of the main shaft.
- The eccentricity causes the cone head to oscillate between o.s.s. (open side setting) and c.s.s. (closed side setting) discharge opening.
- In addition to c.s.s., eccentricity is one of the major factors that determine the capacity of cone crushers.
- The Cone crushers are equipped with a hydraulic setting adjustment system, which adjusts c.s.s. and thus affects product gradation.
CRUSHER TERMINOLOGY
Feed: The raw material that is to be crushed.
Capacity: The output of the crusher computed in tons per hour (mtph/stph).
Product Size: The size of the screened material.
Liners: The mantle & concave are the crushing members and are commonly referred to as liners.
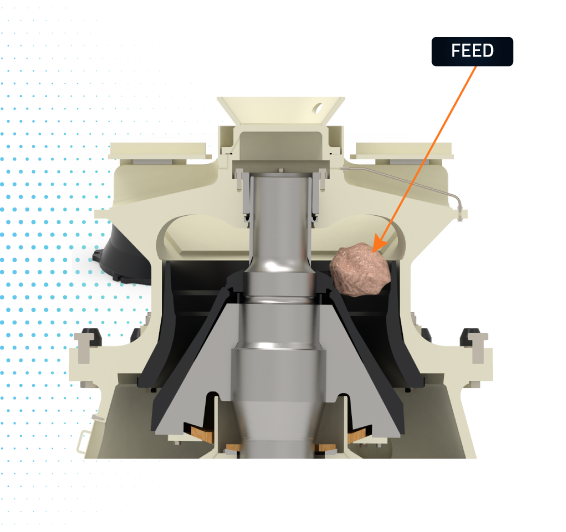
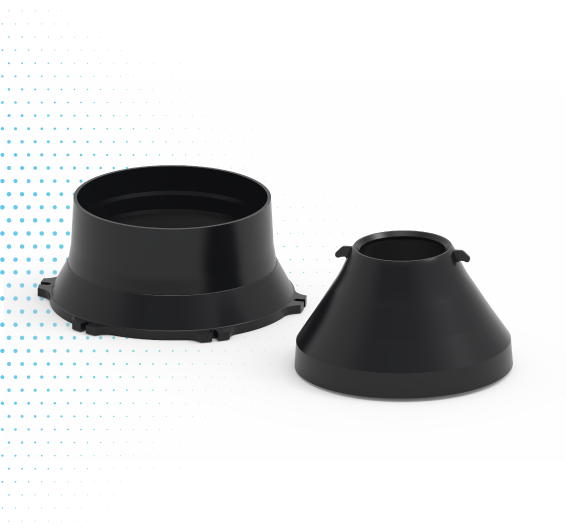
Feed Opening: The largest distance between the top of the crushing members as measured when the two crushing members are at their farthest relationship during one revolution of the eccentric. As a general rule the maximum size of feed should be 60 to 80% of the open side feed opening depending of the crusher type and the raw material to be crushed.
Crushing Cavity: The internal area formed by the two liners.
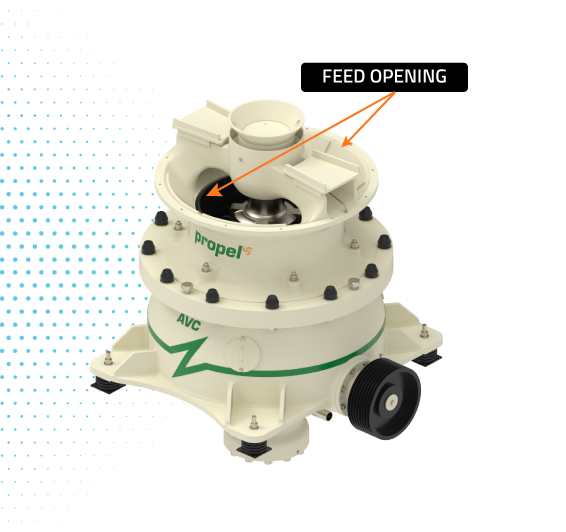
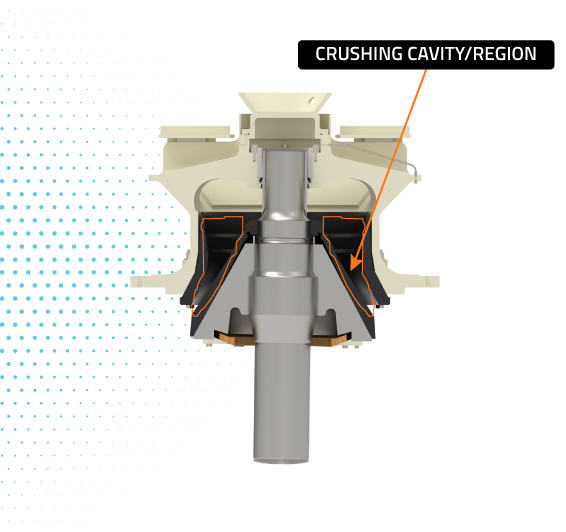
Discharge setting (S): The distance between the bottoms of the crushing members as measured at the point where the two crushing members are at their closest relationship during their gyrating circle (CSS-Closed Side Setting). The discharge setting regulates product sizes.
Minimum discharge setting: The smallest permissible distance between the bottom of concave and mantle as measured at the point where the two crushing members are at their closest relationship during their gyrating circle.
Discharge opening: The distance between the bottom of concave and mantle as measured at the point where the two crushing members are at their furthest relationship during their gyrating circle. This wide opening permits rapid discharge of crushed material.
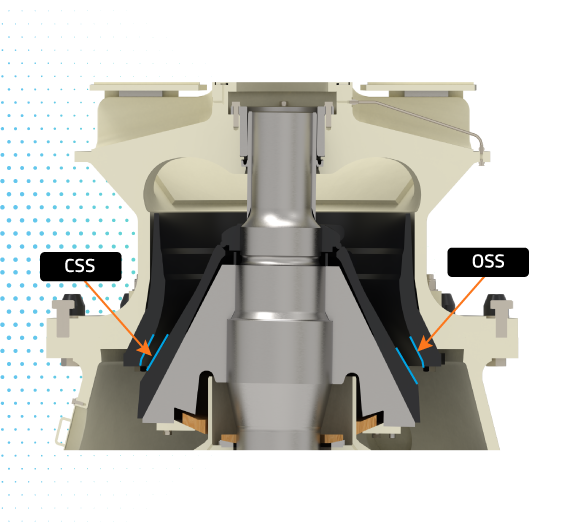
Stroke: The difference between open side setting (OSS) and closed side setting (CSS).
Open circuit operation: The type of operation where precise uniformity of product size is not considered to be of prime importance and the feed is run through the crusher only once.
Closed circuit operation: The type of operation where precise uniformly of the product size is important and the product is screened as it is being discharged and the material which does not pass through screen is returned to the crusher.
SAFETY
Safety of our operators, service engineers and customers has always been our top priority and to ensure that, Propel Cone Crusher comes with
- Limited numbers of service points.
- Special lifting tools are given to ease maintenance.
Cone crushers designed by Propel Industries have the following features for better maintenance
- Closed Side Setting (CSS)
- V Belt change
- Lubrication
- Liners change
We have given set of recommended maintenance procedures in Operation & Maintenance Manual which is absolutely safe to practice.
SALIENT FEATURES
- Sturdy construction – strong in all directions and ensures excellent durability against shock-loads.
- Setting adjustment made with wedge & traditional shim plates.
- Quick and easy installation of Concave & Mantle to the crusher.
- Designed with sacrificial parts to protect the main components of the crusher such as top shell, bottom shell and head. This reduces total lifecycle costs and increases uptime, as it is less expensive to change the sacrificial parts than the main components.
- Ensured top shell, bottom shell, head and main shaft strength by Finite Element Analysis
- IE2 Electric drive motor enabling energy saving
WHY CUSTOMERS OPT FOR OUR CONE CRUSHERS?
- Robust construction design for durability
- Dynamic setting adjustment
- Stable capacity throughout liner life
- Same machine can be used as secondary, tertiary machine with a liner change
- Easy maintenance